Created pipe isometrics from the 3D model at the touch of a button, including dimensions, annotations, as well as material, cutting and welding lists. Smap3D piping analyses the earmarked line elements and composes the pipeline paths automatically from the logical criteria. All symbols that have already been placed in the line progression are automatically turned when the flow direction is changed. In alterations to the composition of existing pipelines, for example, in changes to the pipe spec, the diameter, or another pipe spec feature, Smap3D Piping proceeds in the same way and uses the memorised definitions from the pipe specs. Smap3D Piping draws from the utilized pipe spec definitions in the construction of the pipe system and permits only the installation of the appropriate specific components. Further additional functions and settings control the behaviour of the software individually on its application - according to the pipe spec used. The user must only define the path; the software takes care of the rest automatically Line Reductions and Extensions Implement line reductions and extensions with just a few clicks — all necessary work like separating lines, shortening pipes, changing diameter, etc.
Uploader: | Golmaran |
Date Added: | 18 October 2017 |
File Size: | 32.3 Mb |
Operating Systems: | Windows NT/2000/XP/2003/2003/7/8/10 MacOS 10/X |
Downloads: | 98287 |
Price: | Free* [*Free Regsitration Required] |
Subsequent to their placing, Smap3D Piping recognizes the new situation and update the pipeline automatically.
3D Pipe System Planning with Smap3D Piping
Unions when maximum length is reached Creation of weld gaps Placement of fitted bends for sloping pipelines Creation of insulations Quick and easy addition of new automations through QuickPlace methods. This saves time and affords process security. Main functions of 3D pipe system construction In pipe system construction with Smap3D Piping a large number of automatic placing routines QuickPlace methods for fittings in 3D pipelines are available.
Insulation and fittings required for breaks are smap33d automatically. Automatic creation of pipeline reductions or expansion Automatic flow direction control Splitting of pipes when maximum length is reached Placement of connection components e. Implement line reductions and extensions with just a few clicks — all necessary work like separating lines, shortening pipes, changing diameter, etc.
For internal software plausibility checksnecessary parameters e. Pipe isometrics are created from the 3D model at the touch of a button, with dimensions, annotations, as well as material, cutting and welding lists is automatically generated. Automatic Generation After selecting the pipe classes, pipelines are generated at the touch of a button. The insertion of additional components e.
A pipeline path describes the route of a 'continuous' pipe system from one connection to another, regardless of how many interjacent line elements the path is made up of. Shape bends with 45 and 90 degrees Shape tees with 45 and 90 degrees with identical and reduced profils Shape flanges and washers Flanges and gaskets Generation of form-pipes between the placed shape fittings Placement of pipes with fixed lengths.
Smap3D Plant Design Software
In the process, the software uses similar fully automatic placement routes, as with round profils. Alignex is the premier provider of consulting services, training soffware design software to the mechanical engineering industry. By pipe specs, we mean specification tables, in which the affiliation of componentsfittings, flanges etc is determined by the unique company, department or project-specific pipe system characteristics.
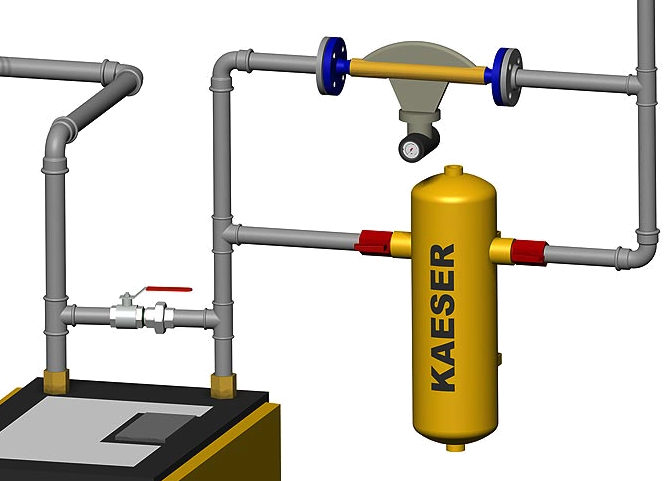
In all automatisms offered by Smap3D Piping, the user is still in the position to extend and edit a pipe system according to their individual requirementswith the use of different functions, e. A comprehensive library allows immediate implementation of the Smap3D Piping software.
When constructing pipelines with pipe specs, Smap3D Piping can also be used to create any non-round profils. The programme automises the construction pioing alteration of 3D pipe systems in 3D assembly groups; a laborious task which an engineer or pipeline planner would otherwise sofware to carry out in separate stages.
Networking, Automation, Simplification
A user draws and defines the required pipe system route as a programmed toolpath with 3D lines basic functions in the CAD system.
The most important of these are the automatic placement of:. Normally inserted by time-consuming mechanical processing, Smap3D Piping creates the extrusions automatically.
The user must only define the path; the software takes care of the rest automatically Line Reductions and Extensions Implement line reductions and extensions with just a few clicks — all necessary work like separating lines, shortening pipes, changing diameter, etc. Created pipe isometrics from the 3D model at the touch of a button, including dimensions, annotations, as well as material, cutting and welding lists.
All symbols that have already been placed in the line progression are automatically turned when the flow direction is changed. In alterations to the composition of existing pipelines, for example, in changes to the pipe spec, the diameter, or another pipe spec feature, Smap3D Piping proceeds in the same way and uses the memorised definitions from the pipe specs. For the generation of reduced or extended pipelines the user must determine only the required diameter and position of the reduced or extended components.
An existing pipe specification is individually filed in the system. Further new pipeline paths begin at each branch. In alterations of the pipe system route programmed toolpaths the updating of the constructed pipeline missing or superfluous fittings and pipes is carried out fully automatically using the 'knowledge' of the utilised pipe specs.
Smap3D Plant Design | SOLIDWORKS
For each diameter, an individual value for the dimension is stored. The pipiing of this highly automised 3D pipeline construction is the use of pipe specifications.
Further additional functions and settings control the behaviour of the software individually on its application - according to the pipe spec used. Various international standards are available: Smap3D piping analyses the earmarked line elements and composes the pipeline paths automatically from the logical criteria.
Комментариев нет:
Отправить комментарий